Welding and heat treatment of P11 Alloy steel pipe
ASTM A335 P11 Alloy steel pipe installation, welding, heat treatment, nondestructive testing
Introduction P11 steel pipe installation process is different from the aspect of ordinary carbon steel installation, including welding, heat treatment and non-destructive testing and other aspects, noting that the P11 steel installation process needs attention and solutions.
1 Introduction
A335 P11 is the ASTM (American Society for Testing and Materials) issued a code-alloy steel, nominal composition of 1.25Cr-0.5Mo. P11 steel pipe mechanical properties obtained in the manufacturing process to ensure that, for the protection of the safe operation of chemical plants, especially the stability of petrochemical industry has a very high temperature and pressure pipes significance.
2.P11 Alloy steel pipe material acceptance
P11 and other chromium-molybdenum alloy steel pipe should have a quality certificate, quality certificates include the following:
1) Material Standard Code
2) material specifications, grade and characteristic data
3) material production batch number and delivery status
4) Name of production
5) test print to check mark
3.P11 Alloy steel pipe. Before using the appearance quality inspection
Before P11 steel pipe should also be checked using the material, size and grade, for visual quality inspection, and meet the following requirements:
1) The surface shall not have cracks, folding, hairline, mezzanine, scarring and other defects.
2) surface rust, scratches and other mechanical damage recessed depth should not exceed the corresponding product standard allows the thickness of the negative deviation.
3) meets the specifications of the logo.
4.P11 Alloy steel pipe welding
(1) welding methods and welding materials
P11 steel pipe commonly used welding method selected TIG and SMAW. Pipe welded joints form two inches above the butt, is generally used welding backing, cover the surface of the arc welding; welding joint form of thin-walled tube is two inches below the socket weld fillet, with full argon welding.
The choice should be based on welding materials to be welded steel chemical composition, mechanical properties and the use and welding conditions into account, workers Comment 09-28 in the choices are ER80S-B2 and wire electrodes E8018-B2. However, for the composition of between P11 and carbon steel or chromium-molybdenum alloy steel and other dissimilar steel welded joints, according to the lower side of the steel alloy content selected welding materials.
The welding electrical characteristics and process parameters of ASTM A335 P11 alloy steel pipe are shown in Table 1 below:
The welding points and welding sequence are shown in Figure 1:
The welding electrical characteristics and process parameters of ASTM A335 P11 alloy steel pipe are shown in Table 1 below:
Table 1 electrical characteristics and process parameters
Number of welding layers | Welding method | Type of welding consumables | Specification of welding consumables(mm) | Welding current | Arc voltage(V) | Welding speed(cm/min) | |
Polarity | Electric current(A) | ||||||
1 | GTAW | ER80S-B2 | Φ2.4 | DCEN | 80~110 | 10~12 | 7~9 |
2 | SMAW | E8018-B2 | Φ3.2 | DCEP | 90~130 | 22~28 | 8~12 |
3~n | SMAW | E8018-B2 | Φ3.2 | DCEP | 90~130 | 22~28 | 10~16 |
The welding points and welding sequence are shown in Figure 1:
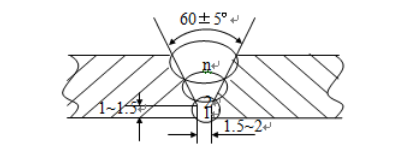
Figure 1
Note: the welding sequence is GTAW priming → SMAW welding 1 ~ n layers in turn.
Note: the welding sequence is GTAW priming → SMAW welding 1 ~ n layers in turn.
(2) requirements for welders
Participate P11 and other chrome molybdenum alloy steel weld welder examination must be carried out according to the provisions of "boiler and pressure vessel pressure pipe welders and management rules." Examination qualified welders welding work to undertake appropriate projects.
(3) welding preparation
Before welding groove preparation, including preparation, assembly and positioning, and no different from ordinary carbon steel welding, and is not described in detail.
(4) welding operations
Welding operation should be carried out within the scope of the welding process requirements. But also for the P11 steel wall thickness greater than 10mm should be preheated before welding, preheating temperature is 150 ~ 200 ℃. After reaching weldment preheating temperature should be timely welding, while maintaining the preheating temperature conditions, each weld should complete a continuous weld. After weldment preheating temperature should be reached in time for welding. After welding the weld should be cleaned up immediately to remove welding slag, spatter, etc., visual inspection.
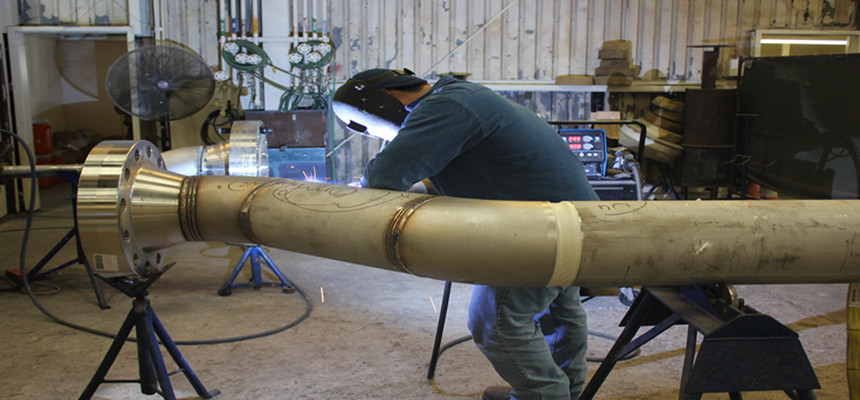
5.P11 Alloy steel pipe PWHT
(1) heat treatment regulations
Chrome molybdenum alloy steel for the P11 and other design documents generally require post-weld stress relief heat treatment should be carried out immediately. P11 steel heat treatment temperature is 700 ~ 750 ℃, the shortest time constant not 2h. Heat treatment at a heating rate and cooling rate, shall meet the following requirements:
1) was heated to 300 ℃, heating rate should be 5125 / T. ℃ / h calculated, and not more than 220 ℃ / h;
2) the temperature of each measuring point during a constant temperature heat treatment temperature should be within the range specified in, the difference shall not exceed 50 ℃;
3) the cooling rate should be constant after 6500 / T. ℃ / h basis, and not more than 260 ℃ / h. After cooling to 300 ℃ natural cooling. (Note: T is the actual thickness of the tube mm)
Heat treatment is not carried out immediately bead after the welding process specification requirements should be 300 ~ 350 ℃ immediately after the time of the heat dissipation hydrogen treatment 10 ~ 15min, and then slowly cooled to room temperature incubation. Before the original welding technology continues to respond again when welded seam welding check to make sure no cracks and other defects, the conditions have post-weld heat treatment.
(2) heat treatment QA
According to the specification requirements, the post weld heat treatment of welded joints, weld and heat affected zone to deal with the hardness value detection. P11 weld and heat affected zone after Brinell hardness after heat treatment should not exceed 225 (see SH / T 3501 specified in Table 10), for hardness testing failed welds should be re-heat treatment. Hardness testing after heat treatment is also a work can not be ignored, it will directly affect the progress of the installation pipe P11.
According to SH / T 3501-2011 regulations to deal with the weld and heat affected zone 100% hardness testing. However, according to GB 50517-2010 "Petrochemical metal pipeline construction quality acceptance" requirement, each time in the heat treatment furnace heat treatment furnace may be 10% of the welded joint checks carried hardness testing [3], which will reduce the workload of part . But for small diameter pipes and corner joints, due to the hardness testing equipment testing work space diameter and difficult to detect, but currently only in use Publicizing Zhenhai area SH / T 3554-2013 "Petrochemical steel pipe welding heat treatment specifications "provides that: indeed due to specification or structural reasons can not be hardness testing of fillet welds and branch connections welded joints, when the construction unit to provide the welding procedure qualification report containing hardness testing qualified, it can be waived hardness testing corresponding welded joints. I think, SH / T 3554-2013 Publicizing use will be on the use and development of P11 steel has played a certain role.
6.P11 Alloy steel pipe NDT
P11 chrome molybdenum alloy steel and other perishable produce delayed crack and reheat cracking tendency of material, non-destructive testing should be completed after 24h and heat treatment is completed both in welding. The proportion of non-destructive testing may refer to SH / T 3501-2011 and GB 50517-2010 Table 12 Table 9.3.1. It should be noted that for the pipeline level SHA1, SHA2, butt welds SHB1 and SHB2 stage pipeline, according to the provisions of SH / T 3501-2011 need for both internal defect detection (detection RT or UT) and surface defect detection (detection method PT or MT), which is different from carbon and stainless steel.
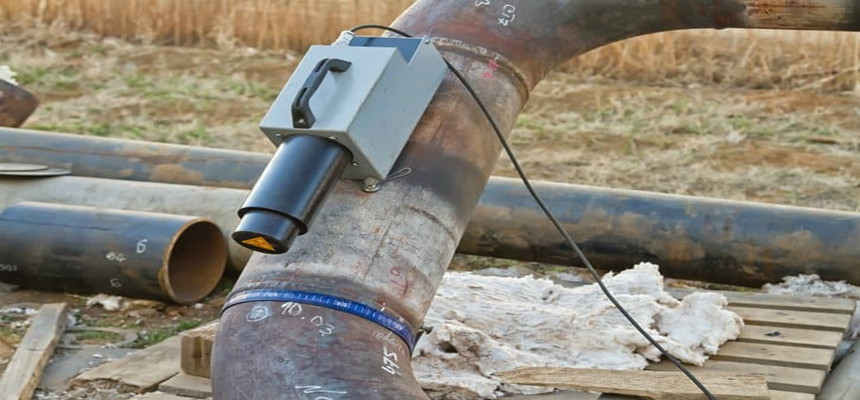
7.P11 Alloy steel pipe construction process Notes
P11 steel pipe in the construction process, the most should pay attention to what happens with the carbon mix, in the event that there are significant security risks at high temperature and pressure conditions. Therefore, in the construction process should be set up specialized materials management personnel, and other special steel P11 according to the relevant provisions of brushing color and full management of P11 steel and other recipients, grant. We should also strengthen the supervision and inspection of the construction site, to prevent the occurrence of mixed material. Another notable is the distribution and use of welding materials, welding materials in order to prevent wrong, specifications SH / T 3501-2011 and GB 50517-2010 provisions are to be extracted at least two welds detect chemical components of each pipeline, current detection methods using rapid spectrometry.